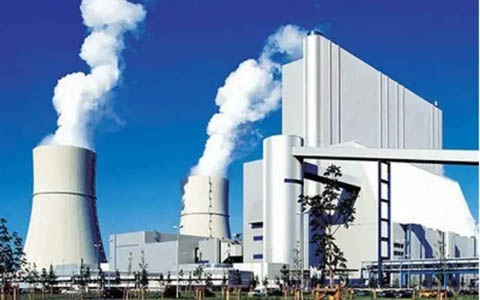
1.1工艺流程
焦炉烟气首先进入干法脱硫系统,利用脱硫剂脱除SO2,然后进入脱硝系统,在还原剂NH3作用下脱除NOx,整个脱硫脱硝过程焦炉烟气温降很低。净化后的烟气经余热锅炉回收后,最后经引风机回送原烟囱排出。
1.2工程应用
该技术已成功运用于内蒙古美方煤焦化有限公司,该公司拥有四座焦炉,每座焦炉产能60万吨/年,每两座焦炉共用一座烟囱,每座烟囱烟气排放量250000Nm³/h,其排放烟气中含有的SO2含量为250mg/Nm³,NOx浓度为1000mg/Nm³。
每座烟囱建设一套脱硫脱硝余热回收一体化装置,分别于2016年6月和8月建成并一次试车成功,目前已平稳运行半年多。处理后的烟气中SO2浓度小于30mg/Nm³,NOx浓度小于150mg/Nm³,不但达到乌海地区环保要求,同时还达到了GB16171-2012《炼焦化学工业污染物排放标准》中表6特殊地区的指标要求,且每小时副产12t0.6MPa低压饱和蒸汽。
1.3技术特点
1)先脱硫后脱硝,最后进行余热回收,脱硫后的烟气中SO2含量较低,有利于减少脱硝催化剂填装量,延长催化剂寿命;脱硫产物属于常规固体废弃物,处理简便,还可以实现资源化利用。
2)首次在实际工程应用中采用干法脱硫,温降很小,远低于半干法脱硫和湿法脱硫,且整套装置除散热外无温降,可保证脱硝时烟气的温度并且有利于最后的余热回收;
3)采用移动床脱硫工艺,且研制出专用脱硫剂,脱硫效率高、压降低;
4)移动床干法脱硫具备高效除尘功能,可大幅度降低烟气中灰尘含量,满足国标的要求,不必另外设置除尘装置;
5)进入余热锅炉的烟气已净化,最大程度地减少了锅炉的腐蚀,延长了锅炉寿命;
6)采用低温脱硝,选用进口的多孔高效低温脱硝催化剂,相同填装量的脱硝效率约为普通脱硝催化剂的2倍,脱硝催化剂填装量少;使用寿命可达3-4年以上。采用CFD模拟对喷氨系统进行设计,最大限度地提高了催化剂效用,降低了氨逃逸;
7)余热回收后的排烟温度高,烟气处理后回原烟囱,使原烟囱始终处在热备状态,也避免大量白烟低空排放;
8)设置了地下原烟道闸板门断电自开启系统,可保证特殊工况下焦炉的安全;
9)整套装置仅有脱硫塔、脱硝反应器、余热锅炉三台主要设备,设备数量少,可灵活布置,最大程度地减少占地面积和投资成本,使得不管是新建一体化装置还是在原有余热回收的情况下扩建脱硫脱硝都变得可行。
2低温有机催化脱硫脱硝除尘一体化技术
2.1工艺流程
烟气经烟道进入反应塔,烟气和循环浆液逆向接触,催化剂捕捉反应产物并形成稳定的络合物,在原烟气氧气(>4%)的作用下,亚砜催化剂络合物与氧气反应生成硫酸、硝酸和亚砜催化剂,硫酸、硝酸与氨水反应生成硫酸铵、硝酸铵,亚砜类催化剂完成一次循环。经过脱硫脱硝的烟气进入高效除尘除雾器,捕获的液滴进入多级气旋设置的一个桶内,脱硫脱硝后的烟气直排。
2.2工程应用
2016年底,该技术应用于山西某焦化厂焦炉烟气的脱硫脱硝项目中。其焦炉烟气流量为320000Nm³/h,SO2含量为100mg/Nm³,NOx含量为800mg/Nm³,温度约为160℃,烟气含氧量为12%。设计要求满足GB16171-2012《炼焦化学工业污染物排放标准》表5中的指标要求。该焦炉烟气脱硫脱硝工程已于2017年6月正式运行。
2.3技术特点
1)在一个塔内同时实现脱硫、脱硝和二次除尘,占地面积小,节省建设投资,生产操作费用低。
2)脱硫脱硝效率高,脱硫率能够达到99%以上,脱硝率能够达到85%以上,可以达到GB16171-2012《炼焦化学工业污染物排放标准》中表5的指标要求,甚至可以达到表6特殊地区的指标要求。
3)产生的硫酸铵和硝酸铵化肥直接进入焦化厂现有的硫铵系统,故无二次污染,无废水排出,同时可以产生一定的经济效益。
4)不需要高温段,更适合焦化厂低温焦炉烟气的脱硫脱硝。
5)该技术采用的独特催化剂在反应过程中会与亚硫酸和亚硝酸形成亚硫酸催化剂络合物和亚硝酸催化剂络合物,防止亚硫酸和亚硝酸逆向分解,生成的亚硫酸和亚硝酸在氧气的作用下形成硫酸和硝酸,硫酸和硝酸与氨水反应生成硫酸铵和硝酸铵溶液。
6)设置的高效气旋除尘除雾器能有效克服氨逃逸和亚硫酸铵、亚硝酸铵气溶胶问题。
7)该脱硫脱硝工艺主要控制的介质为氨水、臭氧和化肥溶液,通过调节臭氧浓度、塔底溶液pH值、化肥溶液浓度等手段就能实现生产的连续、稳定运行。